諾蘭達爐是一種水平圓柱形熔池熔煉爐。爐體在傳動裝置的驅動下正反向旋轉。爐體一端進料,另一端放渣。放渣端沉淀區底部一側開有冰銅出口。煙氣從放渣端爐筒頂部的爐口排出,爐體一側有出風口裝置。
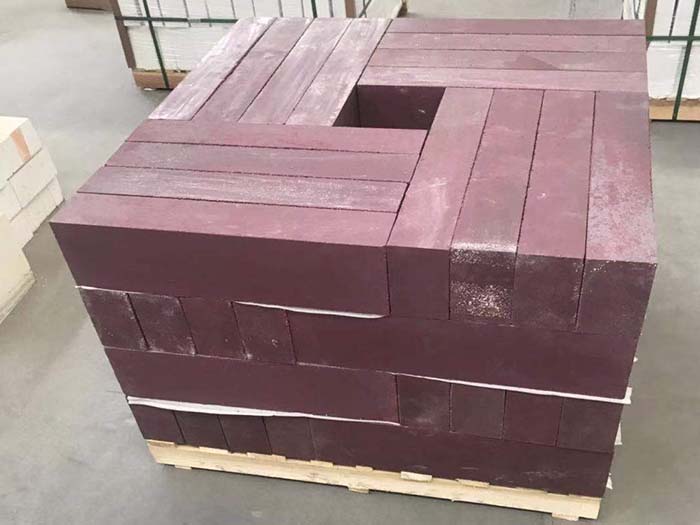
諾蘭達爐的特點
加拿大諾蘭達礦業公司于1964年開始研發諾蘭達煉銅法。
諾蘭達爐具有以下特點:
對原料的適應性較強,既可處理高硫精礦,又可處理低硫含銅材料,既可處理粉礦,又可處理塊礦。
對入爐物料沒有嚴格的要求,不需要復雜的備料過程,原料含水量8%可直接入爐,煙塵率低。
(3)輔助燃料適應性強。諾蘭達富氧熔煉是一種自熱熔煉過程,一般補充燃料率只有2-3%,可以用煤、焦粉、石油焦等低值燃料作為輔助燃料。
(4)熔煉過程熱效率高,能耗低,生產能力大。爐料在生產過程中拋出在熔池表面,立即卷入強烈攪動的熔體中,與吹入的氧氣發生強烈反應,確保爐料迅速完全熔化。諾蘭達爐單位熔池面積處理精礦能力,即床能率可達20-30t/(m2.d)產生高檔銅,減少了下一道工序轉爐吹煉的工作量。產生的煙氣相對較少,煙氣量連續穩定,SO2濃度高,有利于硫的回收,減少環境污染。
(50爐襯無水冷設施,爐體散熱損失小,爐襯設計合理,操作得當,爐壽命可達400天以上。
(6)爐體可旋轉,操作靈活,開爐停爐容易掌握。工作條件好,但爐口和煙罩之間難以嚴格密封,從此漏入空氣較多,導致煙量增加。
(7)爐渣中銅含量高,直接收率低,爐漣需要選礦或電爐貧化。
銅精礦、含銅材料、熔劑和石油焦作為燃料,經配料混合后,由高速拋料機拋入爐內。富氧氣從風口鼓入爐內,使熔池處于攪拌狀態,物料在爐內脫硫和造渣反應,產生含銅量約70%的冰銅。
諾蘭達爐對原料適應性強,熔煉效率高,煙氣中SO2濃度高,能滿足制酸要求。同時,它是一種自熱熔煉技術,能耗低,目前在世界煉銅行業得到推廣。我國大冶冶煉廠正在使用該爐生產銅,生產能力大。
利用高速拋料機將含銅物料和熔劑加入爐內,通過側風口噴灑富氧空氣,保持熔池中的銅和熔渣處于攪拌狀態。精礦中的鐵和硫與氧發生氧化放熱反應,提供熔煉所需的主要熱量。不足的熱量由配有爐料的煤或碎焦補充,或由燃燒裝置的煤或油補充。熔化產生的銅含有Cu55%~75%,銅口間歇放入銅包中,送到轉爐中進行吹煉。爐渣從端墻渣口排出,直接流入渣貧化電爐進行爐渣貧化處理,貧化爐銅也送轉爐吹煉回收銅。或將爐渣放入渣包中,緩冷后送選礦廠,選出渣精礦,渣精礦返回諾蘭達爐回收渣中的銅。反應爐煙氣通過水冷密封煙罩在余熱鍋爐中冷卻回收余熱,或通過其他冷卻方式冷卻煙氣,然后通過電除塵器凈化后送硫酸廠制酸。
諾蘭達爐煉銅屬富氧熔池熔煉,在反應爐中完成干燥、烘烤、熔煉和吹煉造渣工藝,熔煉強度高,熔池攪拌劇烈,為保證工藝順利進行,保證爐子壽命,對爐襯設計和耐火材料提出了很高的要求。諾蘭達爐的易損部位是風口區、爐口、加料端燃燒器和放渣端燃燒器對應的爐筒頂部,以及沉淀區渣線上下圓形墻和渣端墻。
由于大量富氧空氣進入熔體,化學反應劇烈,侵蝕嚴重,爐溫冷熱交替變化,產生頻繁的熱震,以及風眼刺傷引起的機械沖刷,風口爐襯處于極其惡劣的環境中,損壞速度快。因此,風口區爐襯耐火磚的壽命決定了諾蘭達爐的壽命。由于高溫煙氣的沖刷和機械清理爐渣的沖擊,爐口也容易損壞。
沉淀區渣線上下圓形墻和渣端墻,由于處于高溫區,且放渣,放銅形成頻繁的渣層波動,熔渣的嚴重侵蝕和高溫煙氣的沖刷,也容易損壞。在給料端墻的給料口,由于爐料中含有水分和冷空氣,給料口周圍的爐襯變形,給料端燃燒器和給料端燃燒器火焰對應的爐頂圓周爐襯主要由火焰直接沖刷,局部熱負荷過大,大量冷空氣侵入導致熱震。
根據諾蘭達爐的生產條件,要求耐火材料純度高、耐渣性好、強度高、耐沖刷、耐磨、熱穩定性好。以前爐襯主要用兩種耐火磚砌筑:熔鑄鎂鉻磚,建在易損部位,其余部位直接用鎂鉻磚砌筑。
熔鑄鎂鉻磚的用量占總量的30%-40%。隨著爐子設計的改進,一些易損部位的損壞程度有了很大的提高,耐火磚的質量也有了提高。現在用熔粒和鎂鉻磚代替熔鑄鎂鉻磚。熔鑄磚耐磨、耐腐蝕、機械沖刷,但耐急、冷、急、熱性差,價格昂貴。因此,除了幾塊冰銅口外,原本用熔鑄鎂鉻磚砌筑的其他部位已經用熔粒與鎂鉻磚結合,其他部位仍然直接與鎂鉻磚結合。
新聞推薦